Precision Metalworking can be performed in a variety of different ways using a variety of different machinery. Whether the operation utilizes modern-day techniques like CNC (Computer Numerical Control) or if the process is manual, the use of oil and synthetic lubricants or coolants is the cause of many types of airborne pollutants in the Machine Shop environment.
While the use of oil as a lubricant has reduced dramatically over the years, it is still used from time to time. The use of oil in high speed turning or cutting applications usually produces a very fine smoke. This smoke is one of the worst offenders, as the particulate that is generated is very fine and respirable. Since the smoke is wet, it can only be collected in certain types of Filtration Systems.
Only the most efficient Air Filtration Systems will work on the capture and collection of this fine particulate. Listed below are some of the types of Systems that are available.
Most Machine Shops today utilize synthetic or water based coolants to lubricate their Metalworking processes. The use of synthetics has dramatically reduced smoke as a by-product of the process, but still creates a fine coolant mist that can be very harmful to both personnel and machinery. Due to its larger particle size, coolant mist is much easier to capture and collect than smoke and has a wider variety of filtration options.
There are 3 basic types of air filtration technologies that are used on the capture and collection of Oil Smoke and Coolant Mist.
- Centrifugal Type Air Cleaners: Centrifugal units are the least efficient units on fine particulate. They are best utilized for the capture and collection of larger, water based coolant particulate, not the finer coolant and smoke applications. Secondary filtration can be added to these to collect the particulate that passes through the Centrifugal; however, the constant replacement of these filters can be costly. Due to the fact that the Centrifugal is the least efficient filtration method, it is also the least expensive.
|
 |
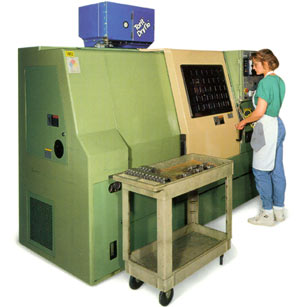
- Media Type Air Cleaners: These units use a series of filters to capture and collect smoke and coolant mist. Most units typically utilize a washable metal mesh filter as a pre-filtration method. This washable and re-usable filter is designed to knock down the larger droplet size particulate, allowing it to drain out of the unit without reaching the more expensive and disposable secondary filter. The second stage is usually a high efficiency bag filter, cartridge filter or box filter. These filters are designed to do the bulk of the work, filtering out the finer particulate. Some applications require a 3rd stage of filtration to capture any of the very fine mist or smoke that might have made its way past the first two stages. The 3rd stage filter is usually a H.E.P.A. (High Efficiency Particulate Arrester) Filter.
- Electrostatic Precipitator: Also known as an Electronic Air Cleaner or ESP. A Precipitator uses high voltage and magnetic attraction to capture both fine and large particulate. The first stage of a Precipitator is a metal mesh filter designed to knock down the larger, droplet size particulate. The next stage is an ionizing section. The ionizer uses high voltage to impart a positive electronic charge to the particulate in the airstream. The next section is a collection component that imparts a negative electronic charge, thus creating a magnetic effect (opposites attract.) to draw the particulate to the Collection Component. Once the charged particles reach the collection component, they stick to the component. Due to the fact that the particulate is wet, a lot of the collected effluent drains off of the components, saving downtime and maintenance of the equipment. An ESP is very efficient and all components are washable and re-usable. Some find this to be a positive feature, as there is little additional cost for change-out of disposable filters; while others find the cleaning requirement to be a maintenance headache.
|